Improving performance and delivering savings at Bakkavor Meals Boston
Bakkavor
Operations and Maintenance
England, UK
.png)
Bakkavor is the leading supplier of fresh prepared food to the major grocery retailers in the UK. F&B manufacturing processes are water-intensive and Bakkavor became an early adopter of water recycling technology through the use of Ultrafiltration (UF) and Reverse Osmosis (RO). They are committed to developing schemes across multiple sites to reduce water consumption.
Alpheus, a UK sister company of CAW, has been operating and maintaining Bakkavor's wastewater treatment plant since 2022. CAW collaborates with Alpheus supporting them with the delivery of several UK operations, maintenance contracts, and projects.
Bakkavor’s main objective was to achieve a sustainable solution whilst creating OPEX savings through proactive plant optimisation, through the option of an alternative contract model. Alpheus was selected based on the track record for delivering cost optimisations from an operational perspective and for our expertise in delivering innovative and sustainable technologies and solutions.
Alpheus committed to delivering:
- Significant process optimisations to improve efficiency;
- Significant reductions in operational costs;
- The required amount of recycled water to reduce mains water demand, with the potential to increase in future;
- Sustained environmental performance;
- Significant reduction in risk to site operations and assurance of environmental compliance.
Project Highlights
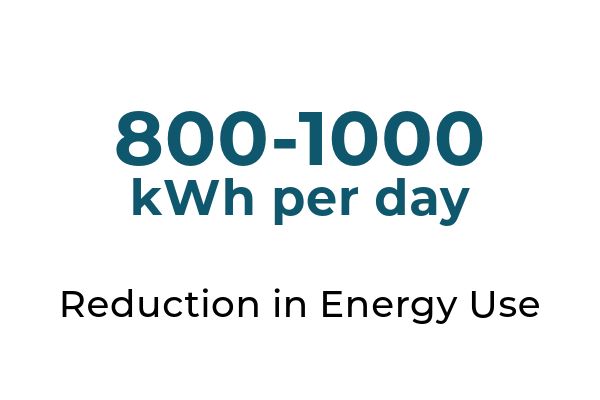
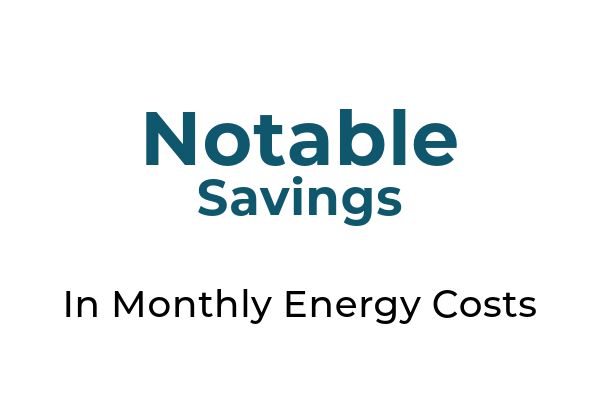
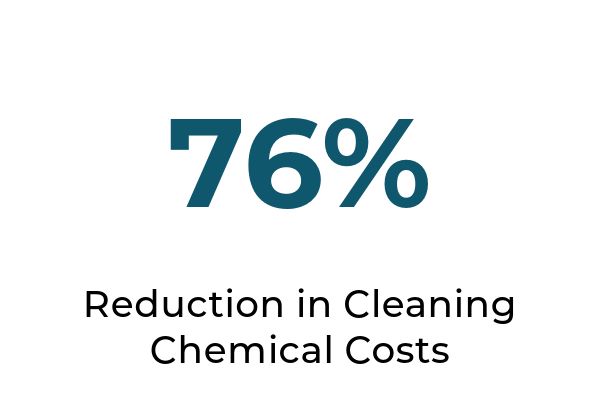
Operations and Maintenance services provided
Alpheus followed a proven onboarding process, concentrating on people and safety in the first instance. Once onboarded, Alpheus focused on operational improvement and optimisation activities.
A thorough and well-resourced transition plan which enabled the smooth and positive integration of the existing Operations team into Alpheus, with minimal risk and no downtime.
- An intensive training and development programme for the incumbent team to enhance their skills to deliver added value and a reduction in overall costs;
- A comprehensive compliance and asset management process to safeguard quality, maximise asset lifespan and reduce risk;
- A specialist team that remotely reviewed data from across all sites looking for unusual trends and improvement opportunities to maintain 100% compliance and optimise performance;
- A continuous proactive and preventative maintenance process focused on continuous improvement to deliver improved reliability and performance;
- Development of an innovation project plan to deliver efficiency, reduce risk and increase safety.
A complete review of the key assets and treatment processes on site to identify areas for immediate improvement. Initial observations highlight an opportunity to reduce chemical costs, and significantly improve the performance of the MBR to cut energy costs.
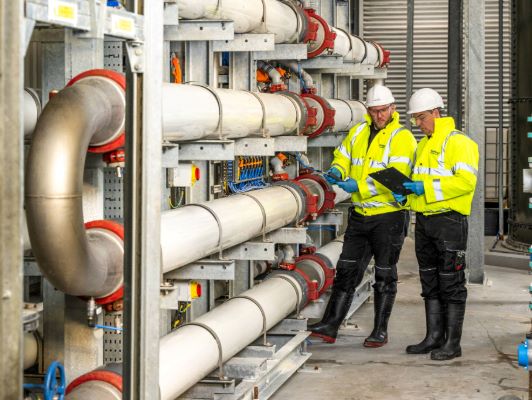
The Outcome
Within just six months of starting the contract Alpheus delivered:
Cost reduction
- A reduction in energy usage by 800-1000 kWh per day which is predicted to deliver significant annual savings;
- A 76% reduction in membrane cleaning chemical costs. This was through a mix of process improvements, reduced membrane operations, better chemical selection and cost optimisation;
- Reduction in sludge disposal costs through better sludge management and by preventing incidents caused by membrane blockages.
Sustainability
- Maintaining provision of recycled water as before with an 800-1000 kWh reduction in energy usage per day.
- A reduction in tanker use for disposal of sludge.
People development
- All members of the team took part in an intensive training programme, benefiting from the knowledge skills and support of the wider team and Anglian Water Group;
- Two members of the team have been able to further enhance their professional development. One has been promoted internally, and the other has taken an opportunity to enhance his skills and knowledge at an Anaerobic Digestion plant we manage.
Talk to us about your next project
.png)